PLA and ABS are the two most popular 3D printing materials. Do you know the advantages and disadvantages of each? We help you choose the best material for your project, in the most complete comparison of PLA vs ABS updated for 2020.
What are PLA and ABS?
PLA and ABS are the 2 most widely used FDM desktop printing materials. ABS was the first material to be used extensively in FDM 3D printing: it is the core material of Stratasys industrial printers, the pioneer of fused filament printing. PLA is the material that comes with the new wave of desktop printers, easier to print on any machine.
Which of the two is more popular? Today, PLA is more used than ABS, but until a few years ago the situation was the other way around. The PLA has imposed itself for its printing ease and finishing in domestic printing and also allows to obtain parts with good mechanical properties. Therefore, PLA is currently the right material for most 3D printing projects. Printing ABS is very difficult on printers that are not prepared for it, so the parts are weaker than if they were made with PLA.
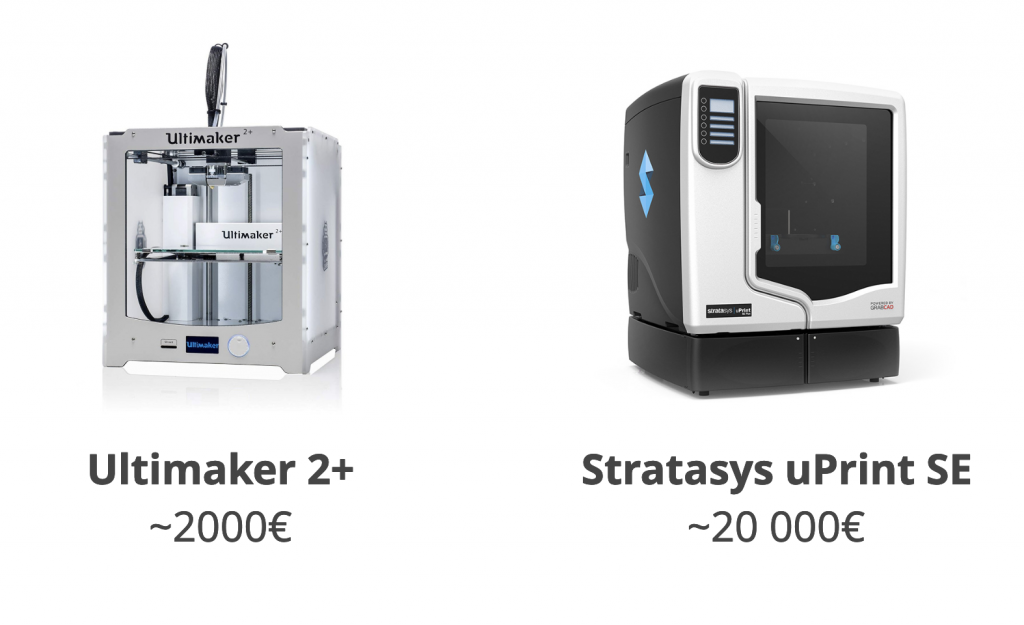
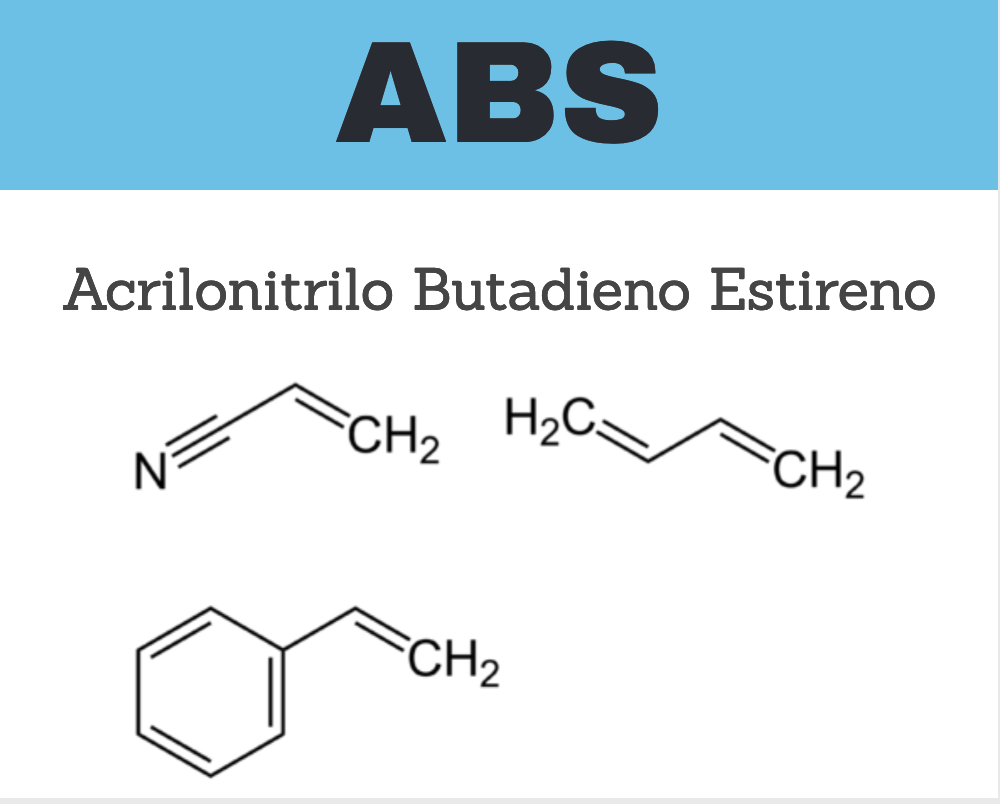
What is ABS?
ABS (acrylonitrile butadiene styrene) is a common thermoplastic well known in the injection molding industry. The most typical example of its use? Everyone has had a LEGO brick in their hand, and that brick is made of ABS.
What is ABS used for?
ABS is traditionally used in industrial printers. It resists temperature better than PLA, but we only recommend it for projects that are going to be smoothed with acetone. For the rest we prefer to use other alternatives.
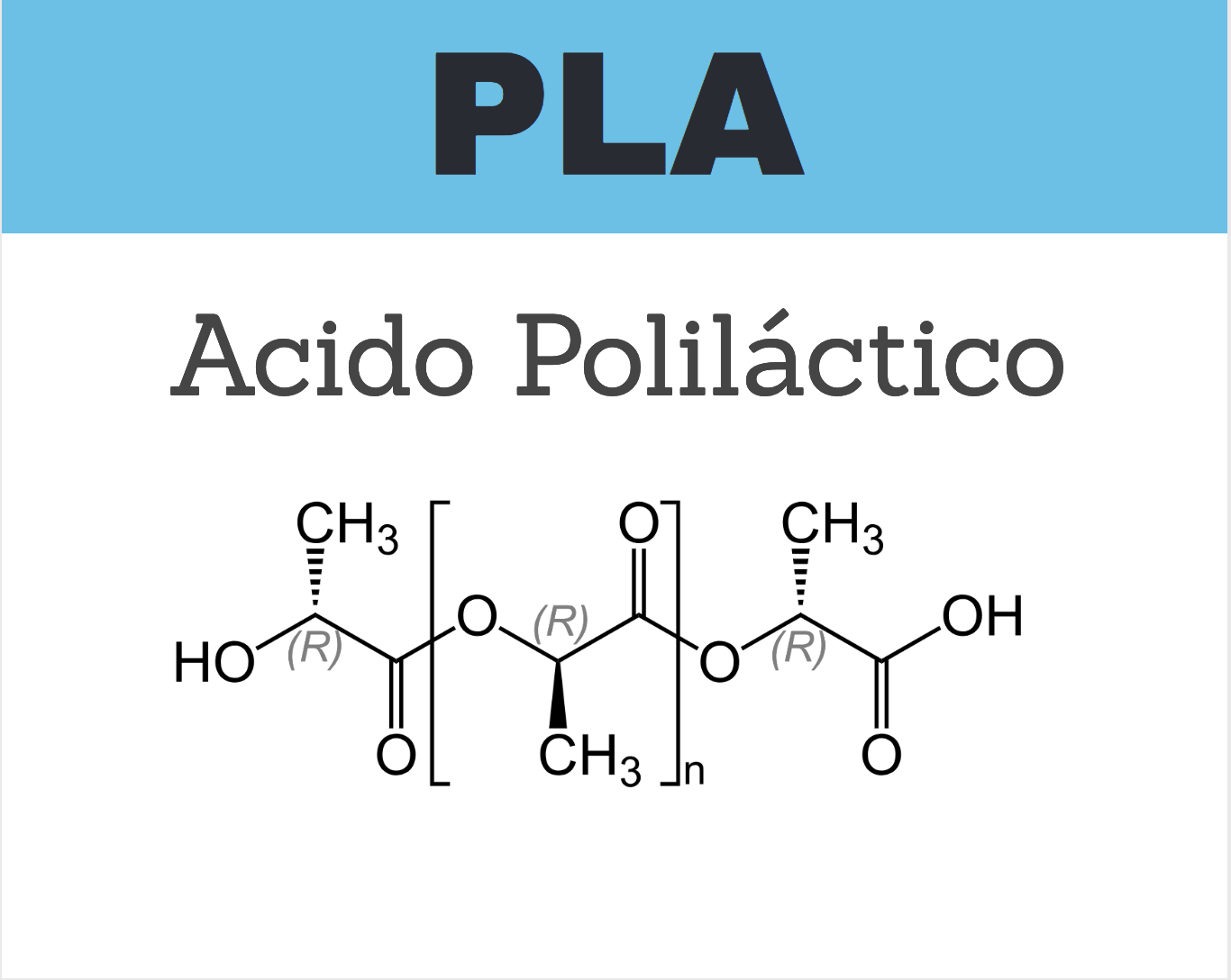
What is PLA?
PLA (polylactic acid) is a biodegradable thermoplastic derived from renewable resources such as corn starch or sugar cane. It is one of the most popular bioplastics, used for many applications ranging from plastic cups to medical implants.
What is PLA used for?
PLA is the most widely used 3D printing material. It is used for generic prototyping and short series where a good finish or price is required. If you need more demanding features, you can always print on PET-G or ASA.
Let’s compare PLA and ABS’ features
The following chart compares the main features of PLA versus ABS:
ABS | PLA | |
Traction resistance | 27 MPa | 37 MPa |
Elongation | 3.5% | 6% |
Flexural module | 2.1 on 7.6 GPa | 4 GPa |
Density | 1.0 a 1.4 g/cm3 | 1.3 g/cm3 |
Fuse point | N/A (shapeless) | 173ºC |
Biodegradable | No | Yes, under the right circumstances |
Glass transition temperature | 105ºC | 60ºC |
Common products | LEGO, electronic casings | Cups, plastic bags, cutlery |
Source: 3D Hubs
Want a more informal comparison of PLA vs ABS properties? Our friend Cesar from Control 3D made a video talking about it:
Finishing and part tolerance
In general, the tolerances and accuracy of FDM-printed components depend largely on the printer calibration and model complexity. Because of its lower print temperature, the PLA, when properly cooled, is less likely to deform (making printing easier) and can print sharper corners and characteristics compared to ABS.
Do you want to print large pieces? In this case you will almost always have to use PLA. ABS is the material most prone to deformation when it cools and, with it, the dreaded warping and cracking. Why? The thermal expansion coefficient of ABS is higher.
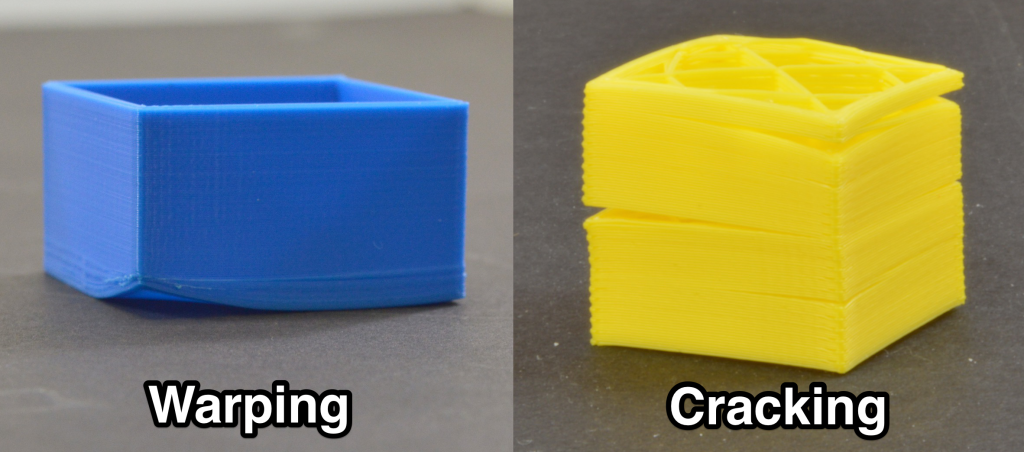
What’s the conclusion? In general, PLA is easier to print and allows for better tolerances and finishing than ABS parts.
Bonus: if you’re looking for the most attractive colors for your pieces, the PLA is usually the best option: all the manufacturers give priority to this material and produce the greatest variety of shades in PLA. That’s why PLA is usually the best material to print pieces that require several colors, as when we talked about 3D key rings made in PLA.
Resistance
With similar traction resistances, ABS and PLA are suitable for many prototyping applications and can also be used in small series.
ABS is often preferred because of its better ductility over PLA. With greater flexural strength and elongation before break, 3D printed ABS can be used for end-use applications, while PLA remains popular for rapid prototyping when form is more critical than function.
Surface finishing and post-processing
The nature of FDM printing means that for both ABS and PLA, the print layers will be visible after printing. Want to see exactly how these layer lines look? We have documented this in our section on the finishing of 3D printing parts.
There is a difference in finishing between the two materials: ABS is normally printed in a matte finish, while PLA is semi-transparent, often resulting in a more glossy finish.
According to the post-processing technique we use:
- ABS can be sanded easily and is often machined (e.g. perforated) after printing. PLA can also be sanded and machined, however, greater care is required in doing so.
- The use of acetone, which is one of the few cases in which we recommend ABS, is often used in further processing to soften ABS, and also gives the part a glossier, smoother finish that disguises the layers.
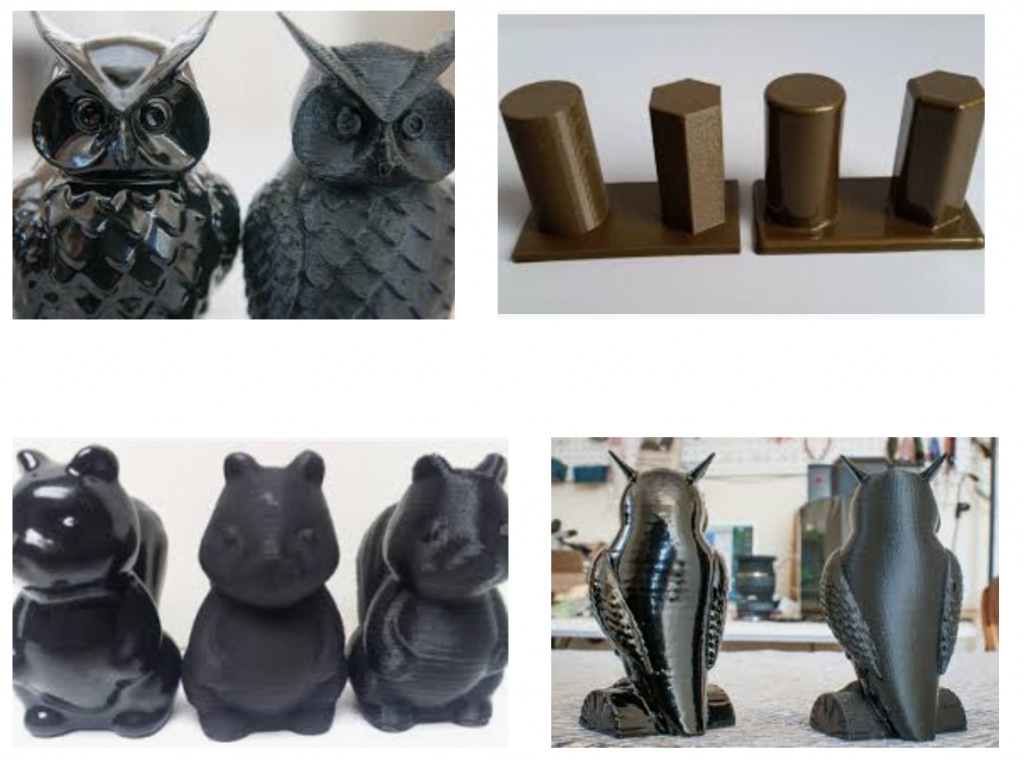
If the aesthetics of a part is critical, for example for a prototype that customers will see, 3D resin printing can always be used for best results.
Heat resistance
For high temperature applications, ABS (105°C glass transition temperature) is more suitable than PLA (60°C glass transition temperature). PLA can quickly lose its structural integrity and may begin to fall and deform, especially if under stress, as it approaches 60°C.
Biodegradability
PLA is stable under general atmospheric conditions and will biodegrade in 50 days in industrial composters and 48 months in water. ABS is not biodegradable, however it is recyclable.
Contact with food
PLA is FDA approved for food use. It is regularly used for the production of food-related items. However, it is recommended that the filament manufacturer confirms that it is safe to do so.
It should be noted that the raw material, PLA resin, is treated in the filament manufacturing plant and additives are added which modify its properties and color. Then it is handled and stored in the form of coils, passes through the extruder and fuser of our printers, is deposited on the bed full of lacquer… Not to mention the roughness and internal cavities of FDM printed parts. For this reason, even if the original resin was approved for food use, it can never be assured that the parts manufactured with PLA are immediately suitable for food use; each case should be evaluated or safety protocols should be established.
PLA vs ABS, conclusions
I hope you liked this comparison between the PLA and ABS. I leave you my personal opinion to choose between them:
- For most projects the best material is PLA. It is the material with the best finishing, the most available colours, the cheapest and for many mechanical properties it is the same or better than ABS. In cases where PLA would not be used it is for parts that will resist temperature, but PETG or ASA can always be used in those situations. These materials improve in mechanical or thermal resistance to ABS and are easier to print and therefore cheaper for you in a 3D printing service like Bitfab.
- ABS, I only recommend it for parts that need to be glued or smoothed with acetone. If you want to use these techniques, go ahead with ABS; for the rest of times you can use PLA or other alternative materials with better features for your project.
I’m glad you’ve read this far. Now is the time to leave me your opinion in the comments. Do you prefer ABS or PLA?