If you’ve been in 3D printing for a while, you’ve certainly gone through all the phases of recycling 3D printing plastic. Over the years, a lot of new projects have appeared that promised to give us the ability to recycle the plastic from our failed prints, media, rafts or purge blocks but, to this day, which of these projects are still standing?
If you want to know the alternatives available in 2020 to recycle the 3D printed plastic, stick around, we’re getting started.
What alternatives are there?
There are numerous ways in which we can recycle this plastic, so we are going to explain the main ones and some examples of each one of them so you can delve into the projects that catch your eye.
The two main alternatives we have are: to recycle the plastic from our prints to turn it back into usable material or to use it to make plastic objects using other technologies such as injection molding.
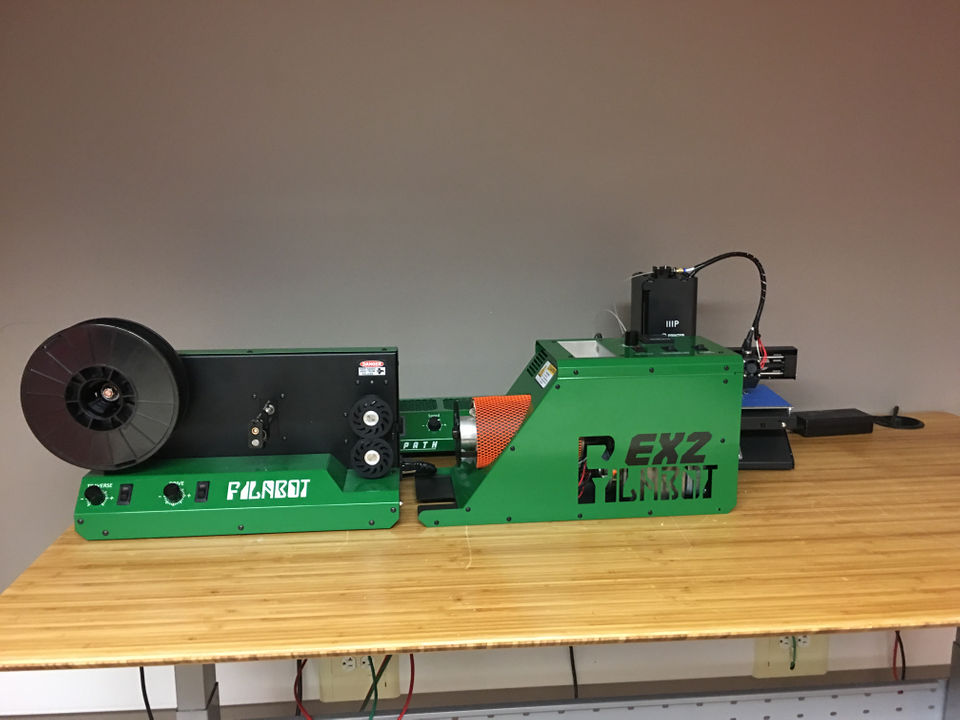
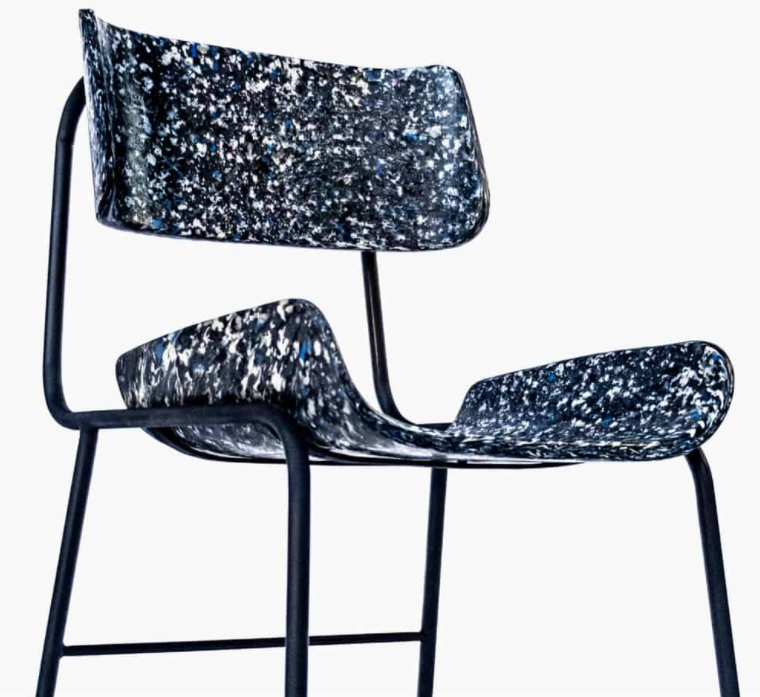
Converting 3D print remainders into new print material
If you want to turn the material left over from your 3D prints back into material you can print on, there are currently three ways to do it: create your own filament, use a special extruder that allows you to print directly using recycled plastic pieces, or buy filament rolls made from recycled material.
Create your own filament
To create your own filament using the remains of other 3D prints there are several machine projects known as filament extruders. Each of these machines works slightly differently, but basically they feed on crushed 3D print debris and melt it down, extruding new filament through a 1.75mm diameter nozzle.
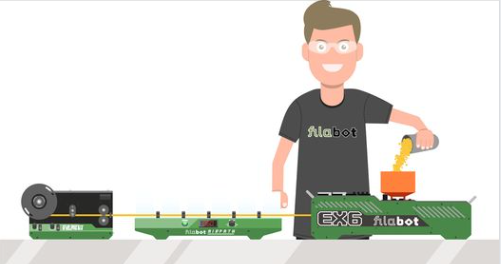
Filastruder
Filastruder is a kit that you can buy for $299 in its most basic version. This product has been releasing new versions and improving for several years, so it is a quite refined equipment and one that can be expected not to give us many problems. If we want to coil this plastic we will also have to buy its filawinder accessory for 169 extra dollars.
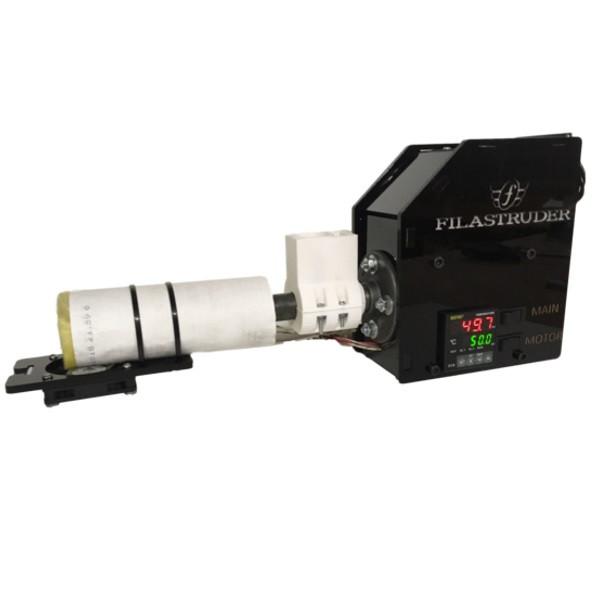
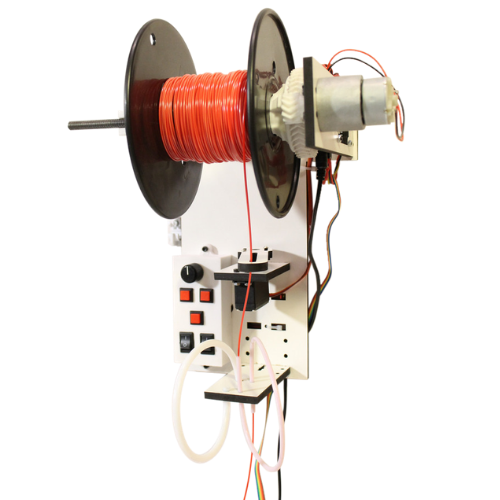
Felfil Evo
Felfil Evo is a much more expensive but also more premium and open source kit. It is available in 3 different kits, a fully assembled and functional one for 719€, a kit for you to assemble for 599€, and a “barebone” kit that only contains the mechanical components but does not include chassis or electronics for 299€. This last option, in addition to the fact that it is open source, is an excellent choice for the more professional makers looking to create their own filament extruder adapted to the needs of their workshop.
They also have a premium pack with the assembled version that comes with a plastic coiling accessory for 1199€.
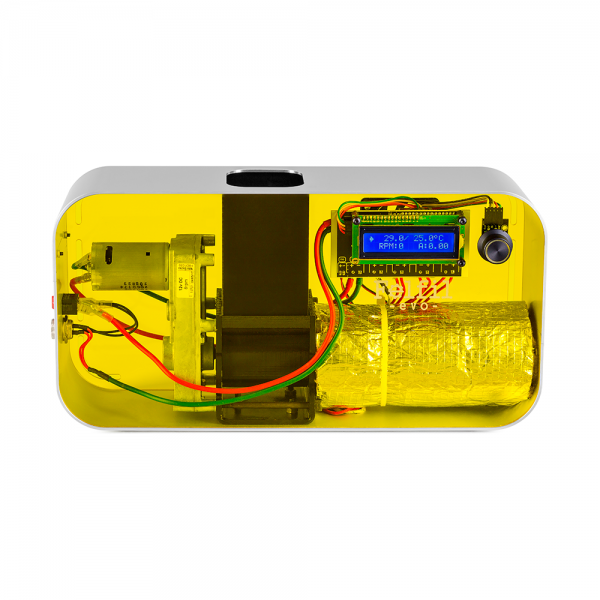
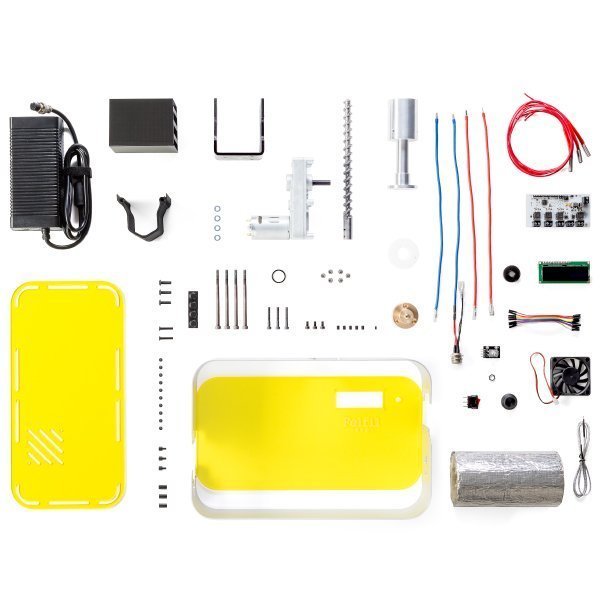
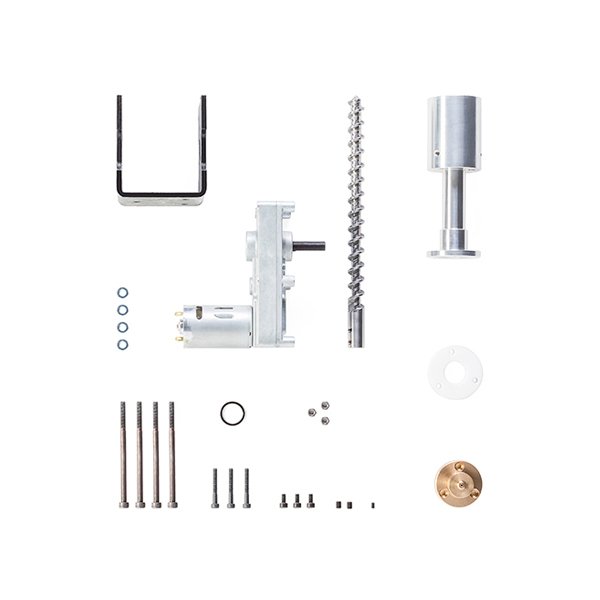
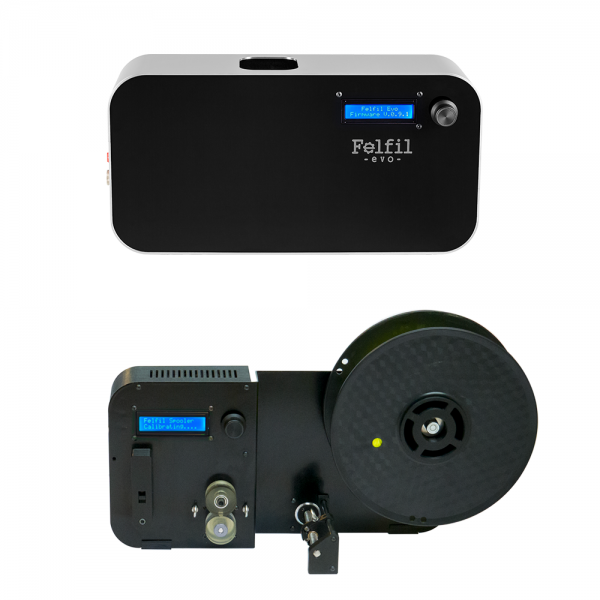
Filabot
Filabot is a brand with a line of products designed to create a complete filament coiling and manufacturing system. These equipments, even in their most basic version, are much more expensive than the previous ones, since they are thought for professionals and not for makers. All equipment comes pre-assembled and tested to ensure a quick and smooth start-up without unexpected complications
There are two product ranges, the Filabot ex2 and the Filabot ex6. The first is the simplest and most affordable, starting from $2699 for the extruder and $4559 for the complete kit including the coiler.
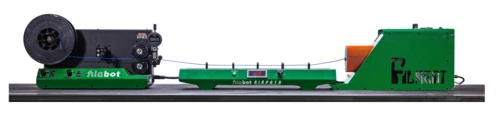
The second one is even more professional and starts at 9899 dollars for the extruder or 10899 dollars for the complete combo.
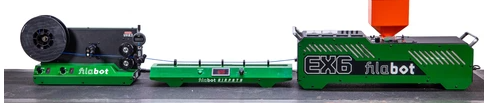
Buy recycled material
If this sounds a bit complicated to you (which it is) but you still want to contribute to the recycling of plastic for 3D printing, then you can buy filament that has been professionally manufactured using recycled material.
Some examples of filaments you can buy made from recycled material are 3RPLAfil or Sakata RE-850.
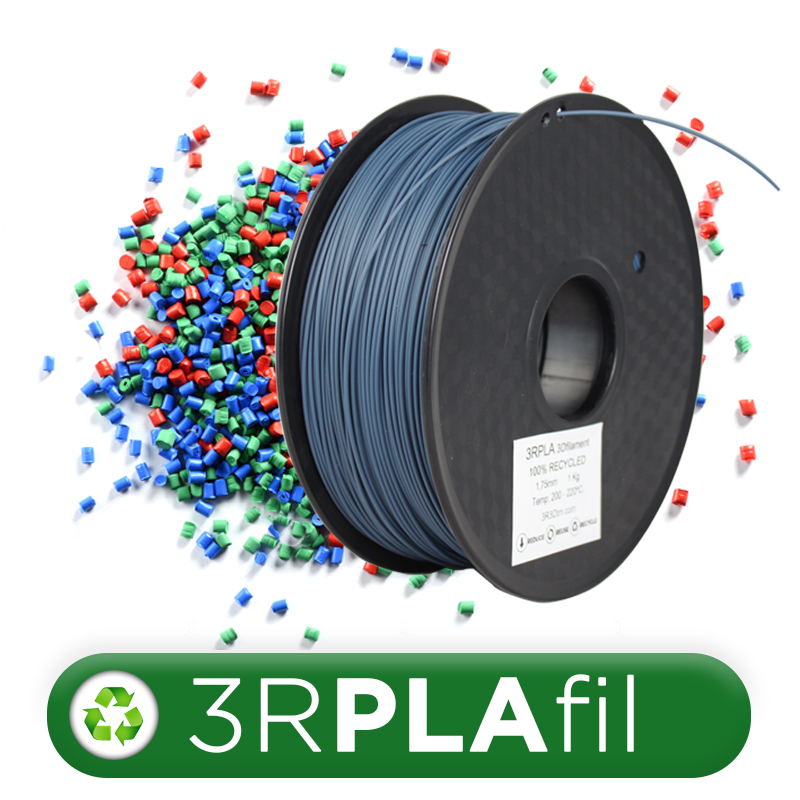
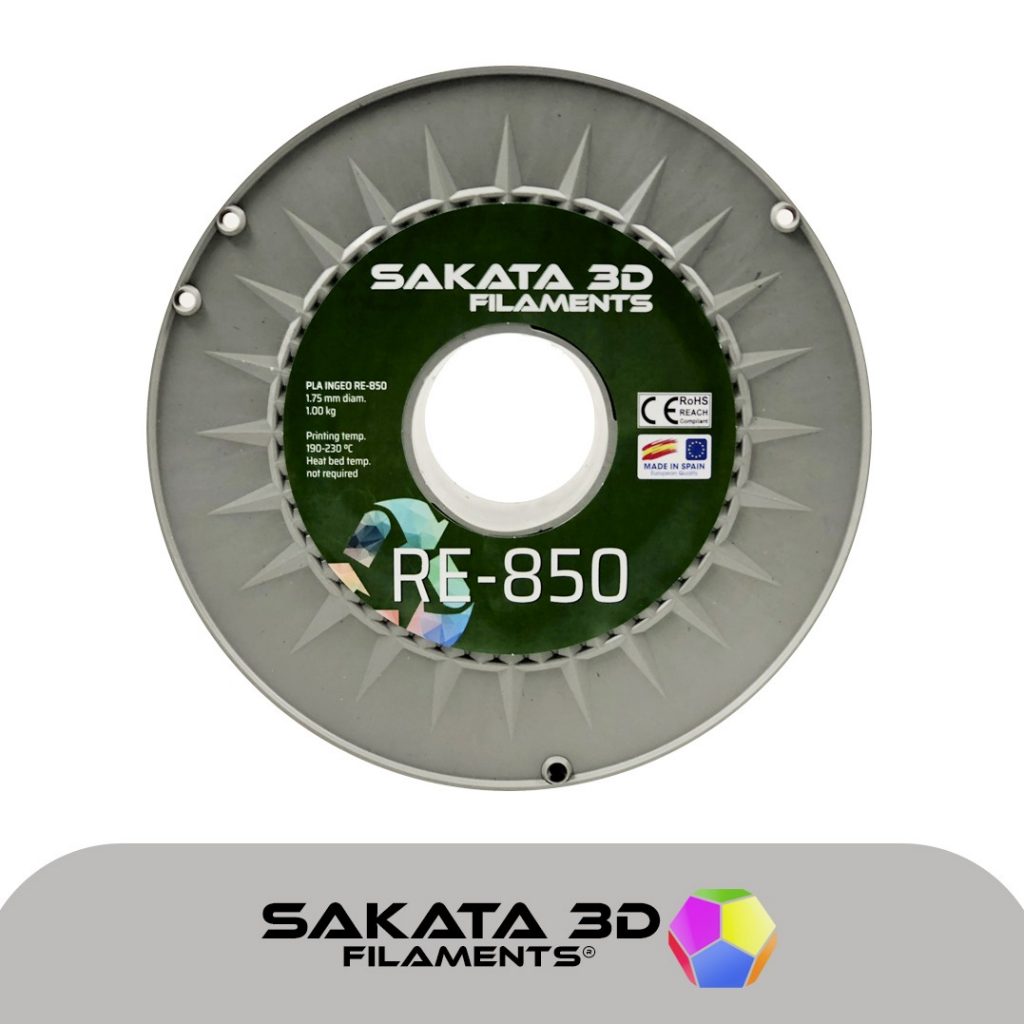
Directly extrude recycled material
An intermediate solution is to use special extruders that you can attach to your 3D printer to print directly using recycled print pieces, without having to go through extruding a new filament. In this field, Spain is the world leader, as a Spanish extruder is the best and most popular extruder of pellets and recycled plastic: the Mahor-xyz Pellet extruder.
This is actually an extruder-melter kit that is placed in our 3D printer replacing the traditional extruder and hotend. It is one of the best solutions, if not the best, as it allows direct extrusion of virtually any type of material from shredded failed prints or pellets that we buy made from recycled material. The list of materials includes: PLA, ABS, TPU, TPE, EVA, PC… In addition, we can incorporate additives such as carbon fiber, glass fiber or kevlar to improve the properties of the material.
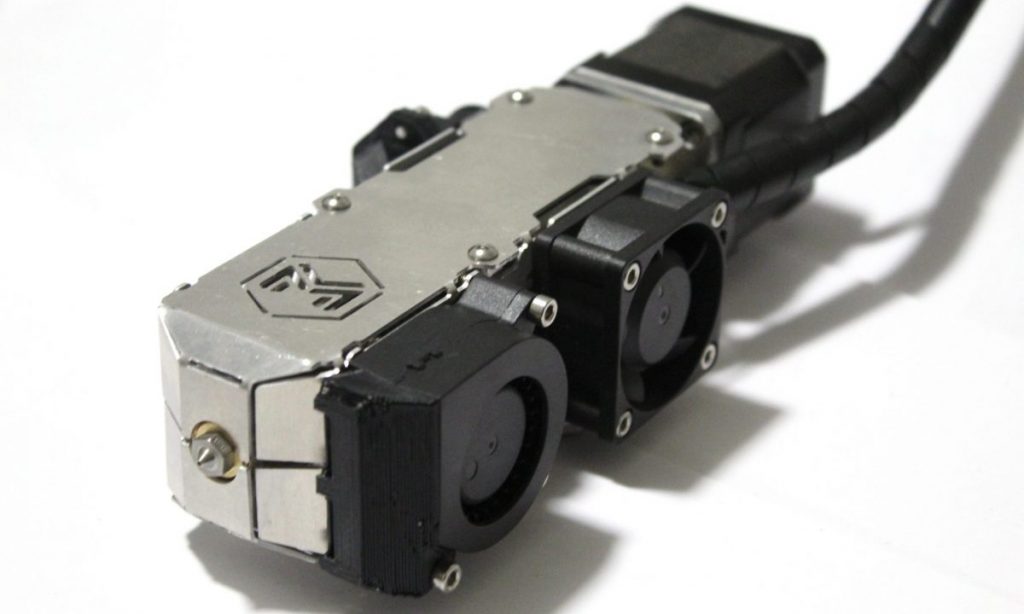
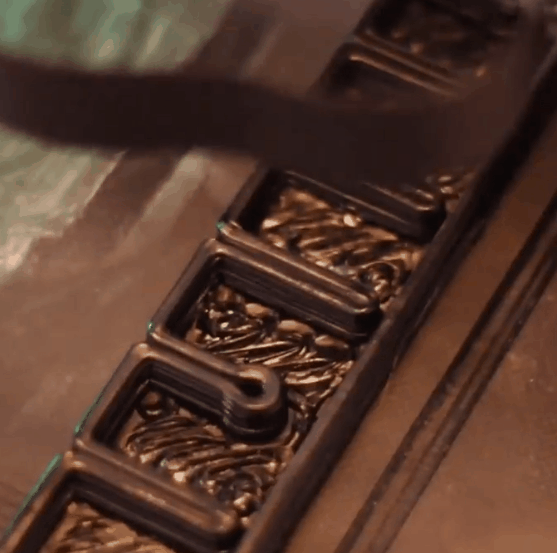
In a future article we will talk at length about this project, as it is a true masterpiece of engineering that will delight the most professional makers in Bitfab.
Making plastic objects
An alternative option to give a second life to the leftovers of our 3D prints is to manufacture objects using techniques such as mold injection. In this respect there is an initiative that stands out: Precious Plastic.
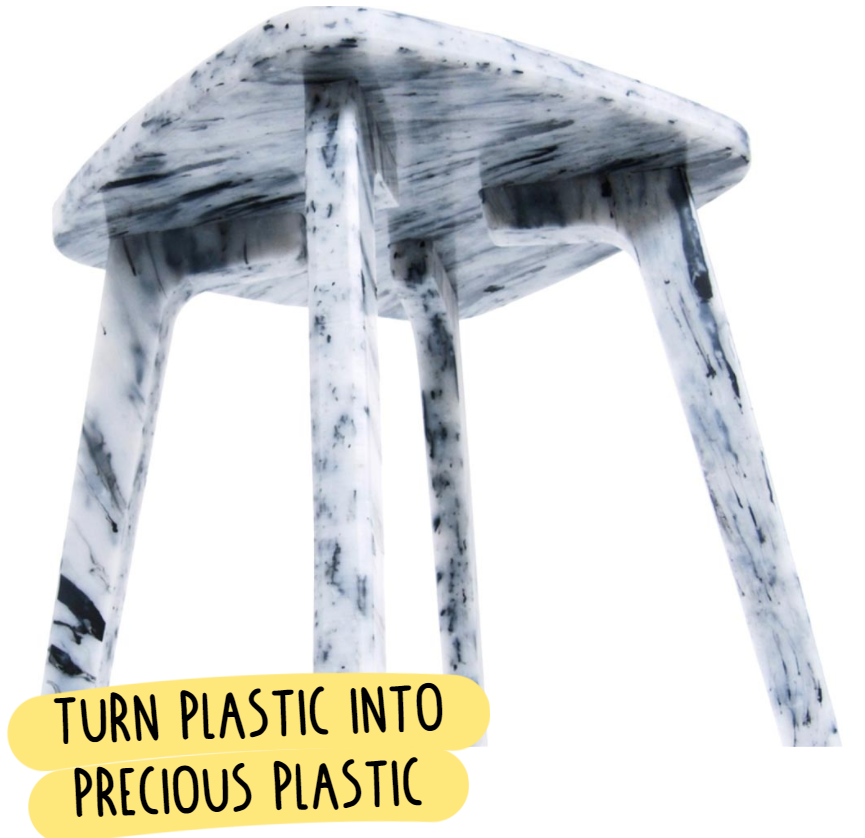
Precious Plastic manufactures everyday objects such as chairs, benches, carabiners, coasters, socket covers or many other things from plastic left over from 3D printing processes.
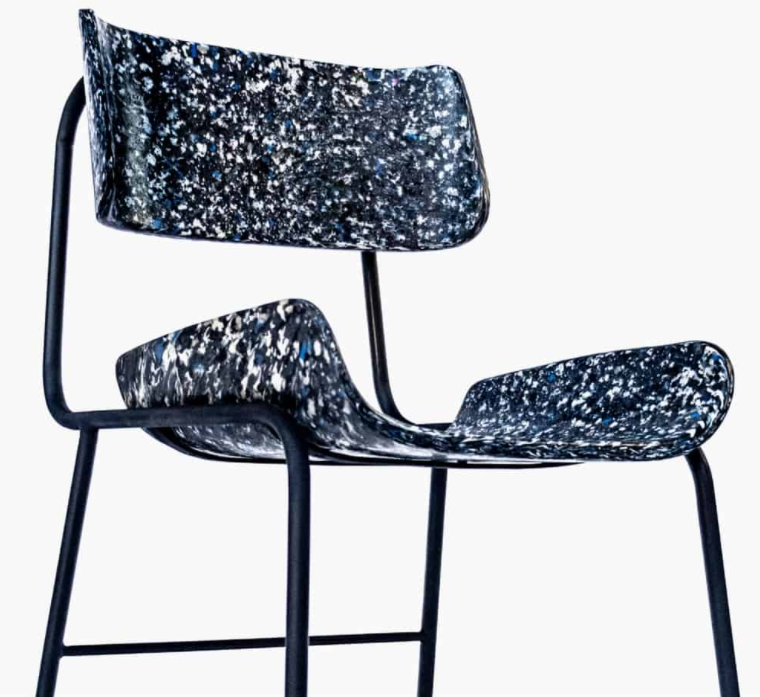
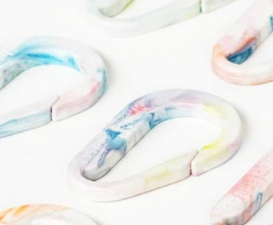
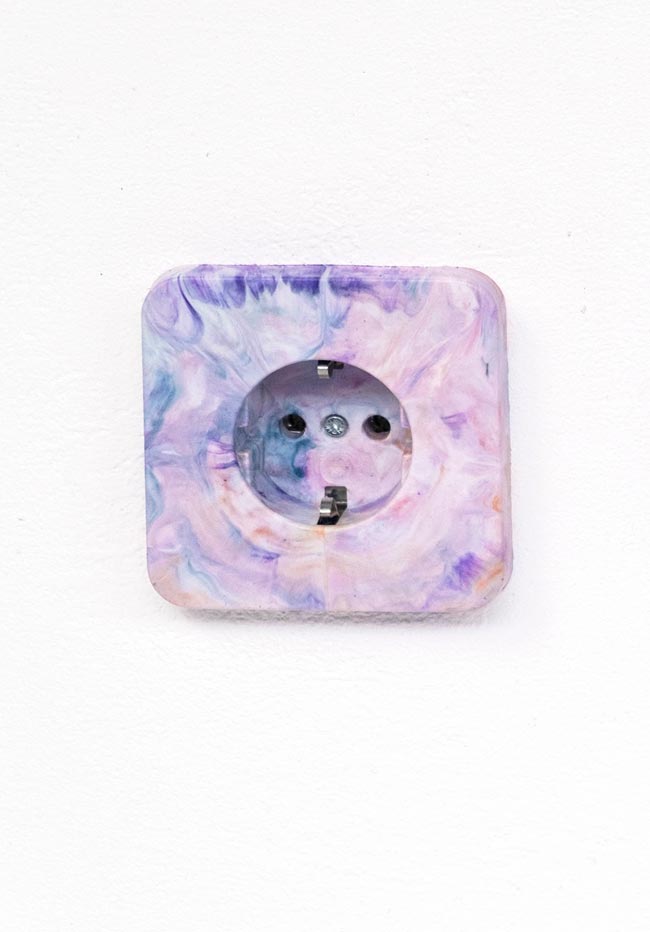
In addition to these objects, they also sell kits with machinery so that you can recycle them yourself.
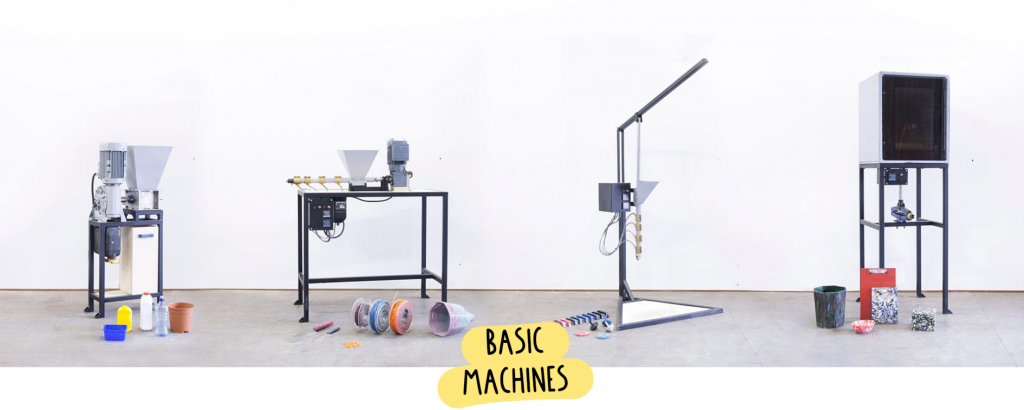
If you want to give a second life to the plastic you print but don’t want to use it to print more things, this is the option that suits you best.
Contact Bitfab
Recycling plastic from 3D printing is a very powerful application and Bitfab can also help you with it.
If you need advice on how to recycle your surplus material or you are thinking of starting a project using recycled plastic, do not hesitate to contact us.